Typical Lycoming O-320-D3G engine overhaul
Typical Lycoming O-320-D3G engine overhaul overhaul process by Nicholson McLaren Aviation
Core Lycoming O-320-D3G engine overhaul received through our goods inward department, where it is processed and issued with a project number and detailing required task through our Aerotrac system. The engine is then transferred to our engine strip department where it is mounted on a purpose-built stand, assigned an engine trolley, that will travel with the engine all through the overhaul process.
A 50+page work pack is generated and populated with the engine details and work scope requirement. All serialised parts received I.E. Crankshaft, Crankcase Carburettor, Fuel pump, Magnetos and Starter motor are recorded.
The Lycoming O-320-D3G engine is then fully photographed, this is logged and filed to ensure all relevant fittings are reinstalled to the correct orientation as received to match airframe configuration on re-installation.
The accessory components for the engine are removed from the engine. I.E. Carburettor, transferred to our in -house fuel systems department for overhaul.
During the Lycoming O-320-D3G engine overhaul, it is completely stripped, with every nut, bolt, washer, and gasket removed. All mandatory replacement parts as detailed in Lycoming SB240 are placed in the unserviceable shelf of the trolley. These parts, including cylinders, pistons, crankshaft main Bearings, crankshaft gear, connecting rods nuts, bolts and bearings, lock washers, gaskets, seals, spark plugs, Harness and Slick Magnetos.
Once disassembled, the engine package is transferred to the engine cleaning bay where all potential parts that can be used are stripped off all paint, oil, carbon and grease.
Once fully cleaned, polished and vapour degreased, the engine package is transferred to the inspection dept.
The Lycoming O-320-D3G engine is visually inspected for corrosion, scores, defects etc on gears, connecting rods, crankshaft, crankcase assembly, including all remaining components to be re-used. These are then dimensionally inspected using UKAS calibrated measuring equipment in accordance with Lycoming overhaul manual 60294-7-14. Any part not meeting the inspection criteria will be tagged and placed on the unserviceable shelf of the trolley. A full AD (Airworthiness Directive) and SB (Service Bulletin) check is carried out to ensure the engine is fully compliant with the latest AD directives and manufacturers SB’s. All replacement parts required added to the project via our Aerotrac our aviation specialist IT operating system. On completion, the engine package is transferred to the NDT dept.
NDT (Non-Destructive Testing) is carried out on the Lycoming O-320-D3G engine, all the Ferrous components inspected on our magnaflux bench I.A.W. ASTM E1444-M11 and Non-ferrous Components inspected on the Dye Penetrant line I.A.W. ASTM E1444-21 for potential sub subsurface discontinuities and defects. Once complete the engine package is transferred to our painting dept.
Each individual engine component is masked individually, areas where a nut or bolt will land is masked separately so when assembled torque is not relieved through paint compression. The engine is then painted to protect from corrosion. Once completed the engine package is transferred to the engine build dept to continue the Lycoming O-320-D3G engine overhaul process.
The Lycoming O-320-D3G engine rebuild is started with the crankshaft on the assembly build stand. The crankshaft, re-bushed connecting rods, camshaft, tappet bodies and crankcase with bearings installed, are dimensionally recorded to ensure all the fits and clearances are I.A.W with the manufactures specifications.
The connecting rods are installed on the crankshaft and new connecting rod bearings, nuts and bolts are installed and torqued up. The torque values are dual inspected by a second certified engineer.
The crankshaft, camshaft and tappets are installed in the crankcase on the bench, the gear backlash and end floats are measured and recorded to ensure they are within specification. The two halves of the crankcase are then sealed together I.A.W Lycoming SI 1125, this is again dual inspected.
The short engine is then re-mounted upon the engine build stand. The internal gear backlash checked and internal timing is set and dual inspected, the oil pump is installed and dual inspected before being installed on the engine.
Once the short motor is complete, we carry out the ring gaps and install the new Lycoming cylinders kits and inter-cylinder baffles. The rocker arms are re-bushed, installed, and dry tappet clearances are checked.
New Champion Slick magnetos are installed and timed to the engine, with dual inspection. A new Harnes and set of sparkplugs are installed.
The carburettor that we have overhauled in-house is installed and the engine and the completed engine is transferred to our purpose-built Dynamometer. During the test all run data is logged I.E: EGT, CHT, Oil temperature, oil pressure, manifold pressure and RPM are captured and recorded.
The engine has a full run I.A.W. Lycoming SI1427C. On completion of test the engine oil is drained the oil filter removed and cut open to be inspected for any potential metal contamination and cylinders are borescope inspected. On completion the engine is transferred back to the engine build department.
The Lycoming O-320-D3G engine overhaul is then prepped for despatched, and final checks completed and dual inspected. The relevant UK CAA, FAA or EASA Form 1 will be raised to requirement.
For a Lycoming O-320-D3G engine overhaul, call us on
+44 (0) 118 973 8011
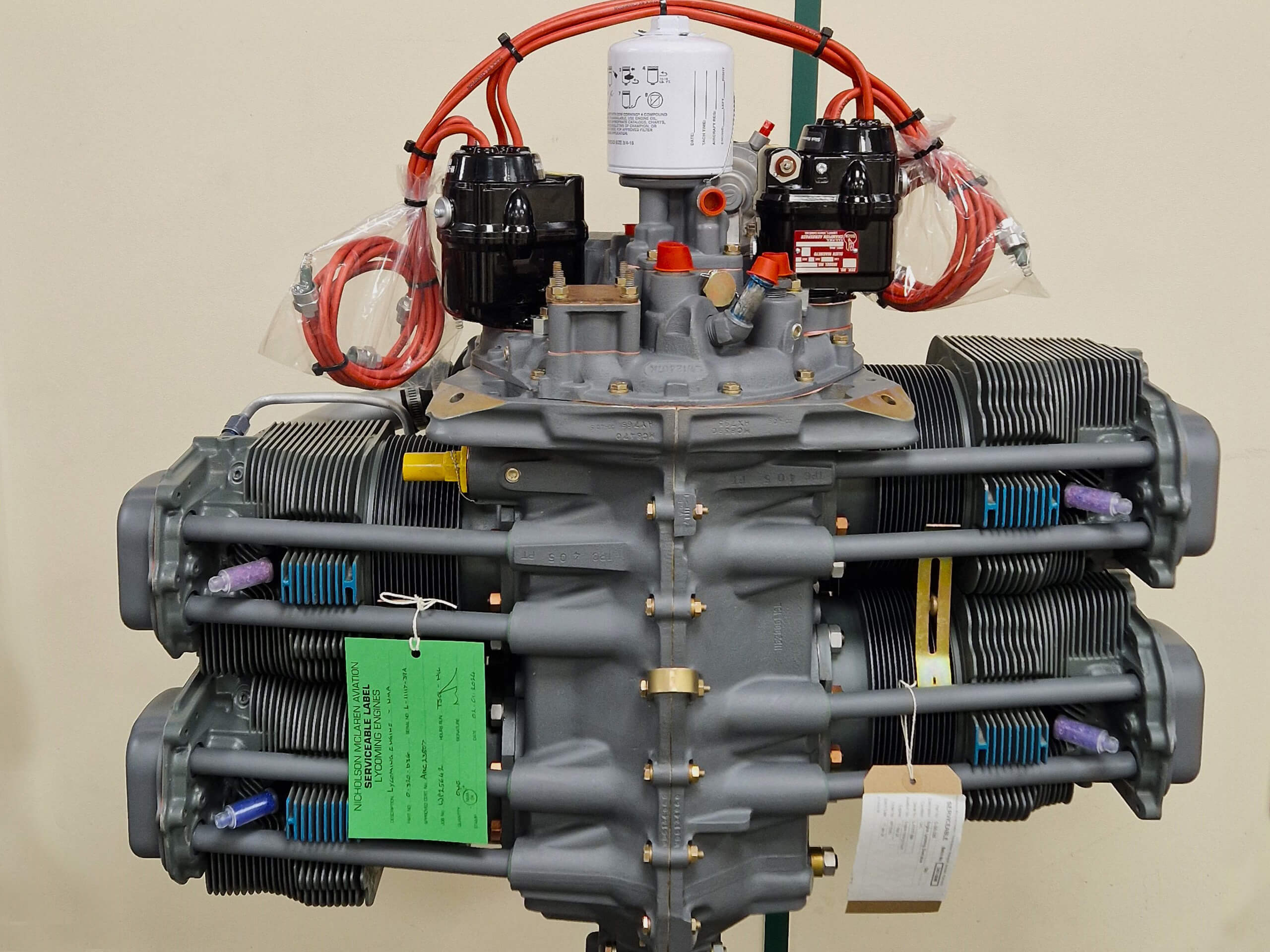
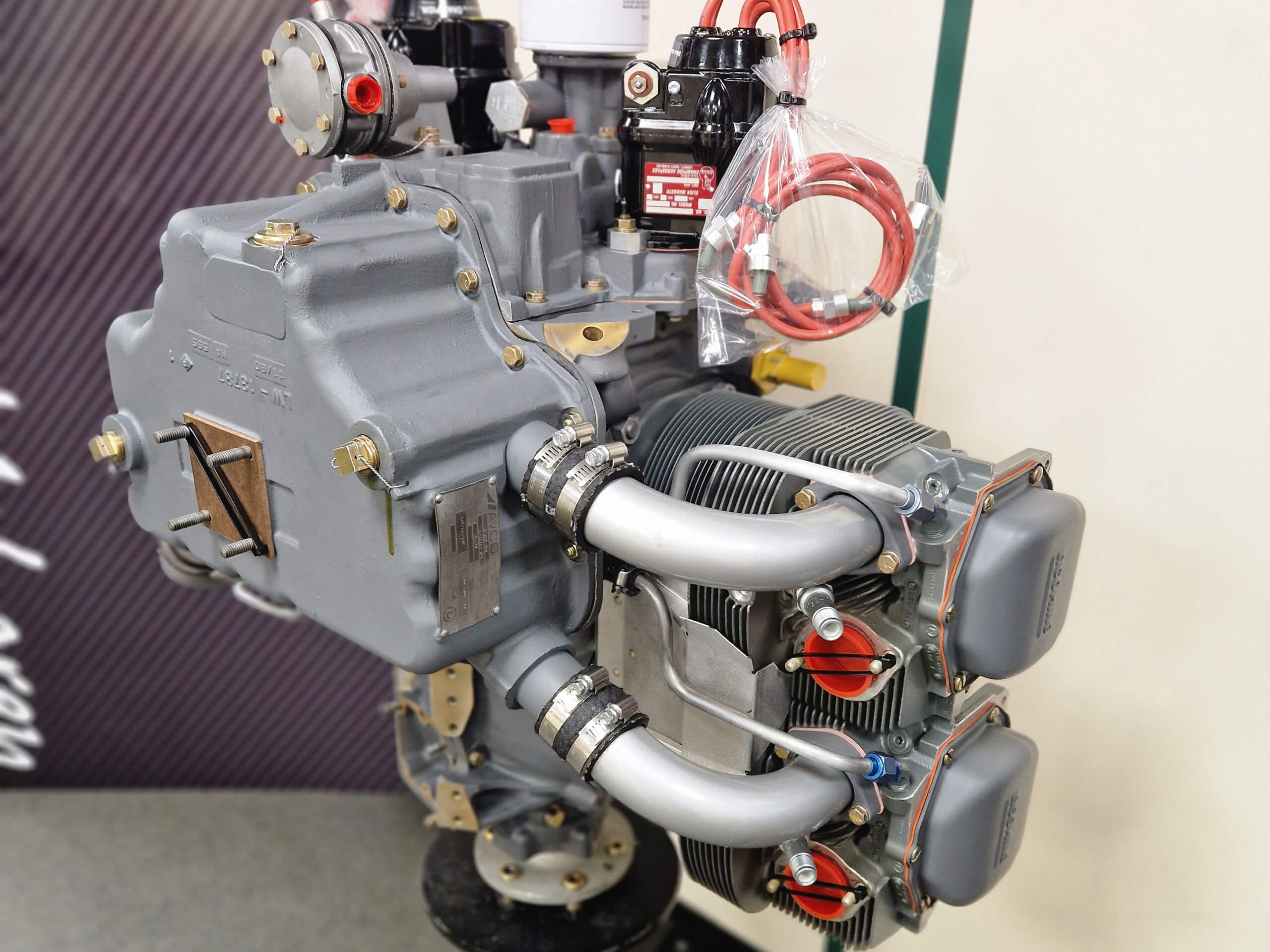
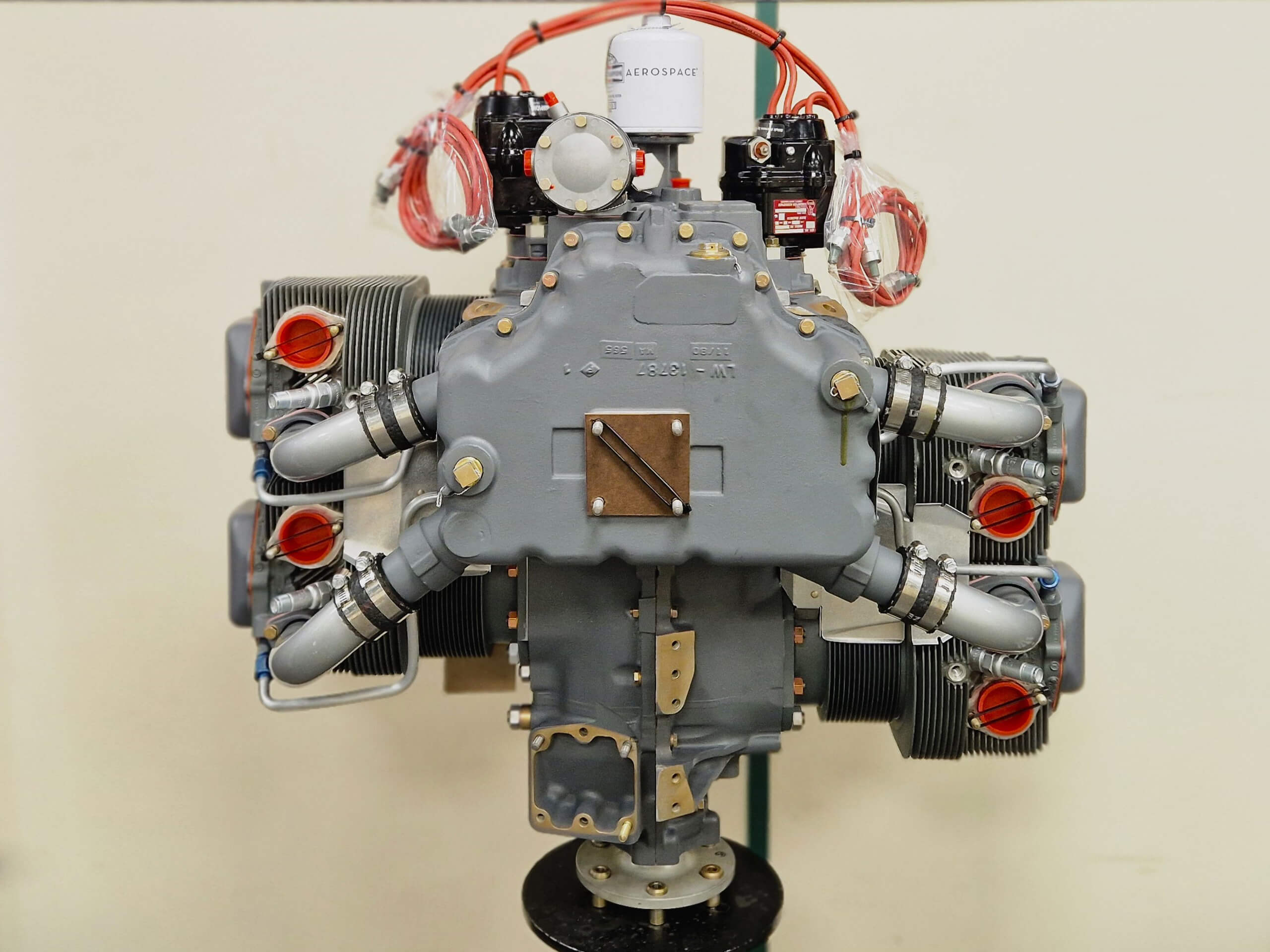
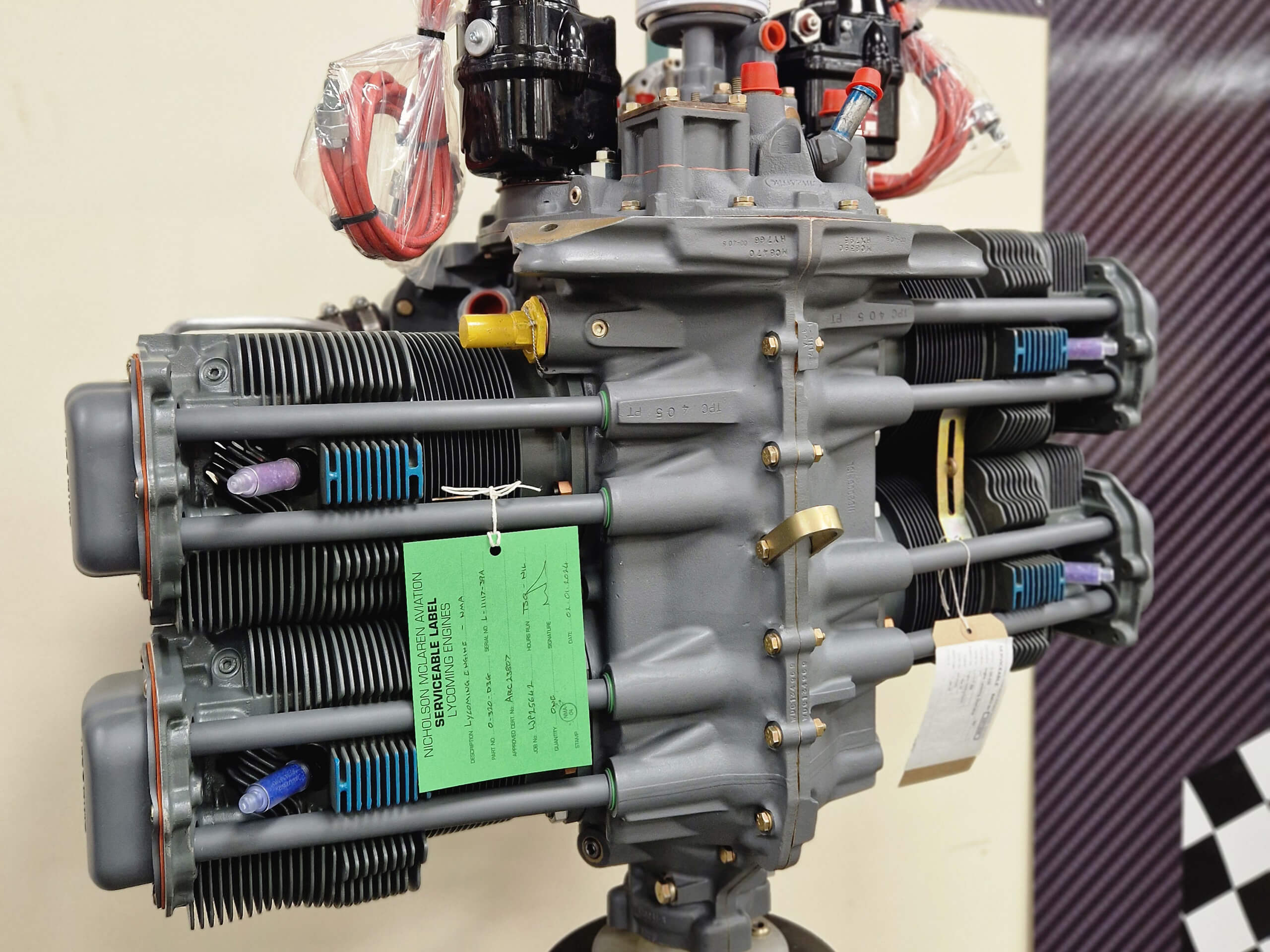
Do you have a question about our aviation services? Call Dean Chamberlain on
Based in Berkshire United Kingdom NMA has the facility, build engines, overhaul existing engines, maintain and repair aviation engines.